图书介绍
磨粒、磨具加工技术与应用【2025|PDF|Epub|mobi|kindle电子书版本百度云盘下载】
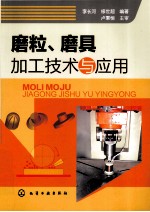
- 李长河,修世超编著 著
- 出版社: 北京:化学工业出版社
- ISBN:9787122150196
- 出版时间:2012
- 标注页数:309页
- 文件大小:98MB
- 文件页数:321页
- 主题词:磨具-金属加工;磨粒-金属加工
PDF下载
下载说明
磨粒、磨具加工技术与应用PDF格式电子书版下载
下载的文件为RAR压缩包。需要使用解压软件进行解压得到PDF格式图书。建议使用BT下载工具Free Download Manager进行下载,简称FDM(免费,没有广告,支持多平台)。本站资源全部打包为BT种子。所以需要使用专业的BT下载软件进行下载。如BitComet qBittorrent uTorrent等BT下载工具。迅雷目前由于本站不是热门资源。不推荐使用!后期资源热门了。安装了迅雷也可以迅雷进行下载!
(文件页数 要大于 标注页数,上中下等多册电子书除外)
注意:本站所有压缩包均有解压码: 点击下载压缩包解压工具
图书目录
第1章 磨粒加工的历史及发展趋势1
1.1 磨粒加工及其历史1
1.1.1 磨粒加工的定义及在国民经济中的重要地位1
1.1.2 磨粒加工的历史2
1.2 磨削加工的特点和磨削过程6
1.2.1 磨削加工的特点6
1.2.2 磨削加工的分类7
1.2.3 磨削加工的基本参数8
1.2.4 磨削过程9
1.3 磨削加工的力和热10
1.3.1 磨削力10
1.3.2 磨削热和磨削温度11
1.4 磨削加工的发展趋势12
1.4.1 磨削加工机理研究的发展趋势12
1.4.2 磨削加工向数控化、自动化、智能化及虚拟化方向发展13
1.4.3 磨削加工新工艺的发展13
1.4.4 硬脆材料磨削技术的发展15
1.4.5 磨料、磨具的研究和开发16
1.5 磨削是否会被硬切削替代17
1.5.1 硬切削工艺17
1.5.2 硬切削会取代磨削加工吗18
1.6 国家科技重大专项在磨削方面解决的重点问题和相关的研究进展19
1.6.1 解决的重点问题19
1.6.2 研究进展20
第2章 磨料与磨具21
2.1 普通磨料21
2.1.1 普通磨料品种及代号21
2.1.2 普通磨料粒度、粒度组成及标记21
2.1.3 刚玉系磨料26
2.1.4 陶瓷微晶刚玉磨料27
2.1.5 碳化物系磨料28
2.2 超硬磨料28
2.2.1 超硬磨料品种及代号28
2.2.2 超硬磨料的应用特点30
2.3 固结磨具31
2.3.1 普通磨料磨具31
2.3.2 超硬磨料磨具42
2.4 涂附磨具58
2.5 磨具特性参数的选择59
2.5.1 磨具的构成及特性59
2.5.2 选择磨具特性参数的一般性原则59
2.5.3 磨具特性参数选择方法的不足与发展趋势61
第3章 砂轮的整形与修锐63
3.1 砂轮磨损的形式及原因63
3.1.1 砂轮磨损形式63
3.1.2 砂轮磨损原因64
3.1.3 砂轮磨损的表征66
3.2 砂轮磨损的测量方法66
3.2.1 用台阶法测量砂轮磨损量67
3.2.2 用仿形法测量砂轮磨损量67
3.2.3 用空气量规传感器测量砂轮磨损量67
3.2.4 用砂轮周围空气流特征测量砂轮磨损量68
3.2.5 用随机过程分析法测量砂轮磨损量68
3.3 砂轮地貌的测量方法68
3.3.1 轮廓测量仪法68
3.3.2 复印法69
3.3.3 光截法70
3.3.4 激光功率谱法71
3.3.5 电镜观察法71
3.3.6 测力计法和热电偶法72
3.3.7 光反射法72
3.4 普通磨料砂轮的修整73
3.4.1 砂轮修整的作用73
3.4.2 车削修整法73
3.4.3 滚压修整法74
3.4.4 磨削修整法74
3.5 超硬磨料砂轮的修整76
3.5.1 电解在线修锐法76
3.5.2 电火花放电修锐法78
3.5.3 激光修锐法78
3.5.4 软弹性修锐法79
3.5.5 超声波振动修锐法79
3.5.6 研磨修锐法80
3.5.7 游离磨粒修锐法80
3.6 砂轮的平衡81
3.6.1 砂轮的静态平衡81
3.6.2 砂轮的动态平衡83
3.6.3 砂轮的动平衡85
第4章 磨削液及供液方法86
4.1 磨削液的作用、要求和种类86
4.1.1 磨削液的作用86
4.1.2 磨削液的种类及性能87
4.1.3 磨削液添加剂的种类及作用90
4.1.4 磨削液的要求91
4.2 磨削液的动压作用与影响92
4.2.1 流体动压润滑的基本理论92
4.2.2 磨削液的动压作用与影响92
4.3 磨削砂轮气流场及对磨削液的影响92
4.3.1 磨削砂轮气流场的产生92
4.3.2 磨削砂轮气流场的影响93
4.4 磨削液的供液方法93
4.5 磨削液射流特性及有效注入技术96
4.5.1 磨削液射流速度分布场研究97
4.5.2 磨削区气流场对有效磨削液的影响98
4.5.3 有效磨削液的计算与分析98
4.5.4 提高有效磨削液比例的途径99
4.6 磨削液的过滤102
第5章 磨削加工表面质量104
5.1 表面质量概念104
5.2 磨削表面质量对零件使用性能的影响104
5.3 磨削表面粗糙度与波纹度105
5.3.1 表面粗糙度105
5.3.2 波纹度111
5.4 磨削表面和次表面的金相组织变化112
5.4.1 磨削表面金相组织特点112
5.4.2 磨削烧伤的概念及分类113
5.4.3 磨削烧伤对零件工作性能的影响114
5.4.4 避免烧伤的措施114
5.4.5 磨削表层烧伤的测量方法115
5.5 表面加工硬化和表面残余应力115
5.5.1 表面加工硬化115
5.5.2 表面残余应力116
5.6 磨削表面裂纹和预应力磨削120
5.6.1 磨削表面裂纹120
5.6.2 预应力磨削121
5.7 残余应力与裂纹的测量122
5.8 其他磨削表面缺陷122
5.9 磨削表面完整性指标综合作用及评价122
第6章 磨削加工精度124
6.1 磨削误差的来源124
6.2 工艺系统受力变形对加工精度的影响125
6.2.1 工艺系统受力变形对加工精度的影响机理125
6.2.2 减少工艺系统受力变形的措施125
6.3 磨削温度及工艺系统受热变形对加工精度的影响126
6.3.1 磨削温度及工艺系统受热变形对加工精度的影响机理126
6.3.2 控制磨削温度和工艺系统受热变形的措施126
6.4 工件和砂轮工作状态对加工精度的影响127
6.5 工艺系统几何精度对加工精度的影响127
6.5.1 机床成形运动误差的影响127
6.5.2 机床传动链误差的影响128
第7章 磨削加工过程的控制129
7.1 磨削加工循环及其控制129
7.1.1 磨削加工的自动化特点129
7.1.2 磨削加工自动循环过程129
7.1.3 自动切入过程的控制130
7.2 磨削过程参数优化130
7.2.1 磨削过程优化的概念130
7.2.2 磨削过程特点与目标函数的设置131
7.3 磨削过程虚拟与仿真132
7.3.1 系统仿真的概念132
7.3.2 磨削加工仿真流程133
7.3.3 磨削仿真数据输入流程133
7.3.4 磨削模型133
7.3.5 磨削加工的虚拟与仿真135
7.4 磨削过程智能控制136
7.5 磨削过程监测与控制136
7.5.1 磨削过程信息监测137
7.5.2 磨削过程信息智能监控技术138
7.6 磨削尺寸自动测量138
7.7 数控磨削139
7.7.1 数控磨床概述139
7.7.2 数控磨削加工工艺140
7.8 机器人磨削141
第8章 常用磨削加工方法142
8.1 平面磨削142
8.1.1 平面磨床的类型142
8.1.2 平面磨削形式及特点143
8.1.3 平面磨削常用方法144
8.1.4 平面磨削常见的缺陷与消除措施145
8.1.5 平面磨削加工实例146
8.2 外圆磨削147
8.2.1 外圆磨削的形式148
8.2.2 外圆磨削砂轮的选择148
8.2.3 工件的装夹149
8.2.4 外圆磨削的方法151
8.2.5 外圆磨削常见的缺陷与消除措施153
8.2.6 轴类零件磨削加工实例155
8.3 内圆磨削157
8.3.1 内圆磨削的特点157
8.3.2 内圆磨削的形式158
8.3.3 砂轮的选择158
8.3.4 工件的装夹159
8.3.5 内圆磨削的方法161
8.3.6 内圆磨削常见的缺陷与消除措施162
8.3.7 磨削加工实例163
8.4 无心磨削165
8.4.1 无心磨削的特点165
8.4.2 导轮倾角、转速与工件转速的关系165
8.4.3 无心外圆磨削的成圆分析166
8.4.4 无心磨削的方法167
8.4.5 无心磨削的用量171
8.4.6 无心外圆磨床的调整171
8.4.7 无心磨削常见的缺陷及消除措施173
8.4.8 无心外圆磨削加工实例175
8.5 齿轮磨削175
8.5.1 齿轮磨削方法和特点175
8.5.2 砂轮的选择和平衡176
8.5.3 磨削余量的确定177
8.5.4 磨齿误差产生原因与消除方法177
8.5.5 加工实例178
8.6 成形磨削180
8.6.1 成形砂轮磨削法180
8.6.2 仿形磨削法(靠模法)180
8.6.3 成形夹具磨削法180
8.6.4 成形展成磨削法181
8.6.5 数控加工方法181
8.6.6 成形砂轮的修整181
8.6.7 磨削加工实例182
8.7 刀具磨削183
8.7.1 刃磨刀具的基本原则183
8.7.2 刃磨刀具常用机床附件183
8.7.3 刃磨刀具砂轮的选择184
8.7.4 刃磨刀具的缺陷及消除措施185
8.7.5 加工实例185
8.8 花键轴磨削188
8.8.1 磨削矩形花键的方法188
8.8.2 花键轴磨削时砂轮的选择188
8.8.3 花键轴磨削时的注意事项189
8.8.4 花键轴磨削常见的质量问题及防止措施189
8.8.5 花键轴磨削加工实例190
8.9 螺纹磨削191
8.9.1 螺纹磨削方法191
8.9.2 砂轮的选择与修整192
8.9.3 螺纹磨削产生的误差及消除方法194
8.9.4 加工实例195
第9章 高效率磨削198
9.1 高效率磨削基本原理198
9.2 重负荷磨削198
9.3 高速强力外圆磨削199
9.3.1 高速强力外圆磨削的原理及特点199
9.3.2 高速强力外圆磨削设备及关键技术199
9.4 缓进给磨削199
9.4.1 缓进给磨削原理199
9.4.2 缓进给磨削的技术特点200
9.4.3 缓进给磨削设备及关键技术200
9.5 高效深切磨削201
9.5.1 高效深切磨削的原理及应用特点201
9.5.2 高效深切磨削对机床的技术要求202
9.6 高速与超高速磨削202
9.6.1 高速与超高速磨削的原理及特点202
9.6.2 高速和超高速磨削的关键技术203
9.6.3 超高速磨削在高效率磨削中的应用207
9.6.4 超高速磨削在难加工材料磨削加工中的应用207
9.7 快速点磨削209
9.7.1 快速点磨削相关技术与机床特点209
9.7.2 快速点磨削的材料去除机理212
9.7.3 快速点磨削的应用特点212
9.8 砂带磨削213
9.8.1 砂带磨削的特点214
9.8.2 砂带磨削的应用214
9.8.3 砂带磨削方式215
9.8.4 砂带磨削的关键技术及参数选择216
9.8.5 强力砂带磨削220
9.9 超硬磨料砂带磨削222
9.9.1 超硬磨料砂带结构与特性222
9.9.2 超硬磨料砂带的分类223
9.9.3 金刚石砂带磨削的应用223
9.9.4 CBN砂带磨削的应用223
9.9.5 超硬磨料砂带的发展趋势223
第10章 精密超精密磨粒加工224
10.1 精密超精密磨粒加工技术的内涵224
10.1.1 精密超精密磨粒加工技术的界定224
10.1.2 几个重要概念224
10.1.3 精密超精密磨粒加工特点225
10.1.4 精密超精密磨粒加工方法及其分类225
10.2 精密磨削加工225
10.2.1 精密磨削加工机理225
10.2.2 精密磨削加工影响因素225
10.2.3 精密磨削的工艺参数226
10.3 超精密磨削加工227
10.3.1 超精密磨削加工机理227
10.3.2 超精密磨削加工影响因素227
10.3.3 超精密磨削的工艺参数228
10.4 镜面磨削228
10.4.1 镜面磨削的定义228
10.4.2 镜面磨削表面的形成机理228
10.4.3 实现镜面磨削的工艺方法229
10.4.4 实现镜面磨削磨床应具备的条件229
10.4.5 镜面磨削的工艺参数229
10.5 在线电解修锐超精密镜面磨削技术230
10.5.1 在线电解修锐镜面磨削的特点230
10.5.2 在线电解修锐镜面磨削实现条件231
10.5.3 在线电解修锐镜面磨削效果232
10.6 双端面精密磨削技术232
10.6.1 双端面精密磨削加工机理232
10.6.2 双端面精密磨削加工装置232
10.7 珩磨233
10.7.1 珩磨的工作原理233
10.7.2 珩磨头233
10.7.3 珩磨油石的选择234
10.7.4 珩磨工艺参数的选择235
10.7.5 珩磨常见的工件缺陷、产生原因及解决方法237
10.8 研磨239
10.8.1 研磨的加工机理239
10.8.2 研磨加工的特点240
10.8.3 研磨加工的分类240
10.8.4 研磨加工的实现条件240
10.8.5 研磨工艺参数242
10.8.6 研磨时常见的缺陷及产生原因242
10.9 抛光242
10.9.1 抛光的加工原理243
10.9.2 抛光加工实现的条件243
第11章 特种磨粒加工方法245
11.1 特种磨粒加工技术概述245
11.1.1 特种磨粒加工的定义245
11.1.2 特种磨粒加工的特点245
11.2 磁力研磨245
11.2.1 磁力研磨的工作原理245
11.2.2 磁力研磨加工的特点247
11.2.3 磁力研磨加工的应用247
11.2.4 五自由度并联机器人磁力研磨加工实例247
11.2.5 磁力研磨加工关键技术250
11.3 磁力悬浮研磨251
11.3.1 磁力悬浮研磨的原理251
11.3.2 磁力悬浮研磨的特点252
11.3.3 加工实例——磁力悬浮研磨加工陶瓷球252
11.3.4 磁力悬浮研磨关键技术253
11.4 磁性流体研磨253
11.4.1 磁性流体研磨的工作原理253
11.4.2 磁性流体研磨的特点253
11.4.3 磁性流体研磨的应用253
11.5 磁流变抛光253
11.5.1 磁流变抛光的原理253
11.5.2 磁流变抛光的特点254
11.5.3 磁流变抛光的应用254
11.5.4 磁流液的组成成分254
11.5.5 磁流变抛光关键技术255
11.6 磨料流加工255
11.6.1 磨料流加工的原理255
11.6.2 磨料流加工的特点255
11.6.3 磨料流加工的应用255
11.6.4 磨料流加工去除速度和精度256
11.6.5 磨料流加工关键技术256
11.7 弹性发射加工256
11.7.1 弹性发射加工的原理256
11.7.2 弹性发射加工的特点257
11.7.3 弹性发射加工的效果257
11.8 浮动抛光257
11.8.1 浮动抛光的工作原理257
11.8.2 浮动抛光材料去除机理258
11.8.3 浮动抛光速度258
11.8.4 浮动抛光的应用258
11.9 动压浮起平面研磨259
11.9.1 动压浮起平面研磨的原理259
11.9.2 动压浮起平面研磨的特点259
11.9.3 动压浮起平面研磨的应用259
11.10 水合抛光259
11.10.1 水合抛光的工作原理259
11.10.2 水合抛光的特点260
11.10.3 水合抛光的应用260
11.11 化学机械抛光260
11.11.1 化学机械抛光材料去除机理260
11.11.2 化学机械抛光的特点261
11.11.3 化学机械抛光的应用261
11.11.4 化学机械抛光关键技术261
11.11.5 化学机械抛光加工装置261
11.12 砂轮约束磨粒喷射加工262
11.12.1 砂轮约束磨粒喷射加工的原理262
11.12.2 砂轮约束磨粒喷射加工的特点263
11.12.3 砂轮约束磨粒喷射加工的应用263
11.12.4 砂轮约束磨粒喷射加工关键技术263
11.12.5 砂轮约束磨粒喷射加工实例263
11.13 磨粒喷射加工265
11.13.1 工作原理265
11.13.2 加工装置265
11.13.3 磨粒喷射加工的分类265
11.13.4 磨粒喷射加工的特点266
11.13.5 磨粒喷射加工的应用266
11.13.6 主要工艺参数267
11.13.7 磨粒喷射加工关键技术及发展方向267
11.14 电解磨削267
11.14.1 电解磨削的工作原理267
11.14.2 电解磨削加工的特点268
11.14.3 电解磨削的应用268
11.15超声波加工268
11.15.1 工作原理268
11.15.2 超声波加工的特点及应用268
11.16电泳磨削技术269
11.17精密超精密特种磨粒加工技术研究热点270
第12章 难磨削加工材料的磨削加工271
12.1 难磨削加工材料的类型及磨削加工特点271
12.1.1 难磨削加工材料的类型271
12.1.2 难磨削加工材料磨削加工的特点272
12.1.3 改善难磨削加工材料磨削性能的措施272
12.2 不锈钢的磨削加工272
12.2.1 不锈钢的种类272
12.2.2 不锈钢磨削的特点273
12.2.3 不锈钢磨削的参数选择273
12.2.4 不锈钢磨削加工实例278
12.3 钛合金的磨削加工279
12.3.1 钛合金的种类279
12.3.2 钛合金磨削的特点280
12.3.3 钛合金磨削的参数选择280
12.3.4 钛合金磨削加工实例283
12.4 高温合金的磨削加工284
12.4.1 高温合金的种类284
12.4.2 高温合金磨削的特点285
12.4.3 高温合金磨削的参数选择286
12.4.4 高温合金磨削加工实例288
12.5 工程陶瓷的磨削加工291
12.5.1 工程陶瓷的性能和特点291
12.5.2 陶瓷磨削的参数选择293
12.5.3 陶瓷磨削加工实例295
12.6 玻璃的磨削加工300
12.6.1 熔融石英玻璃的磨削300
12.6.2 光学玻璃的磨削301
12.7 玛瑙的磨削301
12.8 新高速钢的磨削加工301
12.8.1 新高速钢磨削加工的特点302
12.8.2 新高速钢磨削加工时砂轮的选择303
12.8.3 新高速钢磨削加工时磨削用量和磨削液的选择304
12.9 钢结硬质合金的磨削加工304
12.9.1 钢结硬质合金的性能及其磨削加工的特点304
12.9.2 钢结硬质合金磨削加工时砂轮的选择305
12.9.3 钢结硬质合金磨削加工时的磨削用量和磨削液305
12.10 球墨铸铁的磨削加工305
12.10.1 球墨铸铁材料及其磨削加工的特点305
12.10.2 球墨铸铁磨削加工时砂轮的选择305
12.10.3 球墨铸铁磨削加工的工艺条件306
12.11 铜、铝合金的磨削加工306
12.11.1 铜、铝合金磨削的特点306
12.11.2 铜、铝合金磨削时砂轮的选择307
12.11.3 铜、铝合金磨削加工的工艺条件307
参考文献308
热门推荐
- 3709645.html
- 3698253.html
- 2892295.html
- 2657591.html
- 2264994.html
- 2194186.html
- 1474897.html
- 2589534.html
- 1441721.html
- 531141.html
- http://www.ickdjs.cc/book_2606820.html
- http://www.ickdjs.cc/book_3652147.html
- http://www.ickdjs.cc/book_792156.html
- http://www.ickdjs.cc/book_1425697.html
- http://www.ickdjs.cc/book_1658385.html
- http://www.ickdjs.cc/book_1487414.html
- http://www.ickdjs.cc/book_3430740.html
- http://www.ickdjs.cc/book_1473134.html
- http://www.ickdjs.cc/book_1993013.html
- http://www.ickdjs.cc/book_1206760.html